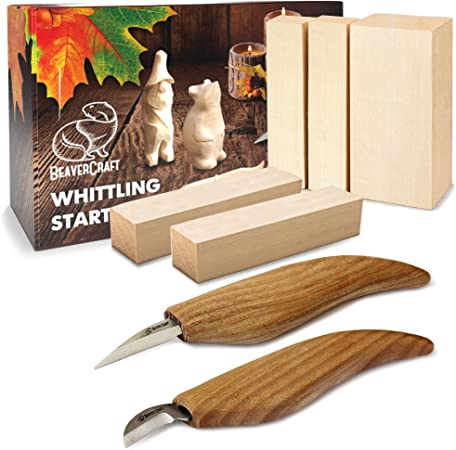
First, choose a piece and then make the required cuts to carve a face in wood. Using a step-by-step video, follow along as the expert guides you through the process. The face can be made more realistic by the progression of the cut. A lifelike face can be created by the progression of the noses on the wooden piece. In addition to the face outline, you may also choose colored dyes and shellac to add a realistic finish.
Hardwoods
First, consider the type of wood you intend to use when carving a wood face. Hardwoods, a type of tree with broad leaves, can grow in different climate zones. They are suitable for many purposes including furniture and building because of their high density, strength and beautiful appearance. Hardwoods can be more cost-effective than softwoods but are durable and fire-resistant.
You might want to try wood carving if you are new to the art. These woods are much easier to work with and are good for beginners. It is important to remember that hardwoods can have the same quality and finish while softer woods are not. You should experiment with different types before you settle on a single type.
Softwoods
The first step to carving a face in wood involves choosing the softwood. Softwoods are often more difficult to carve and have more knots. They are also more likely to crack if you use big strokes. The smallest pieces of wood will be cut by a beginner carver, which reduces the amount of detail. This is not a big problem, but it is something to be aware.
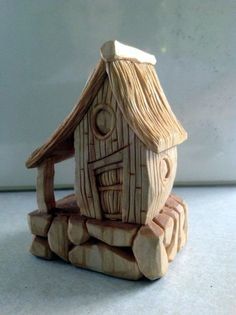
Some hardwoods are easier than others. Aspen, butternut, and basswood are among the easiest to work with. For this reason, it is best to use knives with a steeper bevel. Softwoods also make it easier to work with than hardwoods. This allows you to carve along or against the grain. The quality of the finished product will depend upon the wood you use to carve it.
Colored Dyes
You can create a bright, detailed finish to a wood carving by using colored dyes. You can find these in a wide variety of colors and mix them with water or alcohol to create a unique colour. Use colored dyes that are mixed with shellac to lighten woods. Make sure you ventilate your area after applying the dyes. Paste wax is another option. Be aware that an excessive glossiness may distract from your work. Use 0000 steel wool to remove excess glossiness.
Wood dyes come in many varieties and are easy to use. Wood dyes are compatible all topcoats, and they are easy to use. They solve common finishing challenges. They come in a variety primary colors so they are easy to mix up and apply. They come in many different shades, so you can mix them according to your personal preference. They can also be combined to create unique colors.
Shellac
Shellac should be available before you apply it to your wood carvings. Although you can buy a jar of the stuff, it is easier to use a brush to apply it. A two-pound cut is sufficient. This is because the shellac will gradually build up and will reduce brush marks. A thicker cut is better than a thin one because shellac can be very water-thin. Make a pad from small, golf-ball-sized pieces of cotton and lint-free cloth to ensure you get the correct amount. Then, dip the tip of your brush into the shellac and let the excess flow back into the bottle.
Shellac can add color and highlight grain. Shellac can be mixed with different colors to create custom blends. The lac can even be applied to darken the shade. Shellac, unlike other wood finishes won't turn yellow or become cloudy. It will also last longer, so you can make more faces. And you can do this with any kind of wood carving project!
Gouges
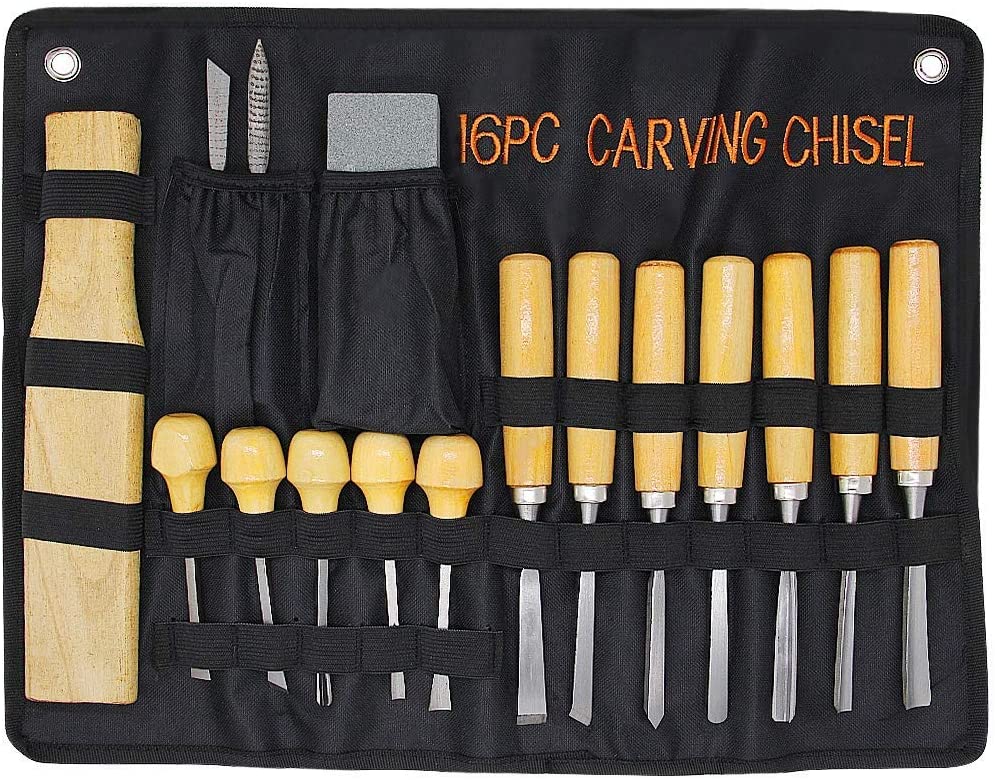
There are many types of gouges. The most common types of gouges are the straight and palm gouges. Straight gouges should be held by hand. While palm gouges have shorter shafts or handles, they can be used with your hands. Hand held carving becomes much easier when the handles are shorter. These palm gouges can also be called veiners. They are perfect for carving faces into wood. Here are a few things to consider before you start carving.
First, it is important to understand how to select the correct gouge. You need a gouge that can carve a shallow groove. A sharp edge and small sweep are essential features of a good gouge. Gouges are commonly classified by size. A 3/10 gouge will make the same-size cut as a 5/10 gouge. The scoop between the edges gets deeper as the first number is increased and the sweep becomes more curvy. A gouge with a small sweep will be able to carve a shallow v-shaped profile.
FAQ
Where can I buy hardwood lumber?
You can buy hardwood lumber at Home Depot. They carry a variety of wood products such as flooring, cabinets, and furniture.
A large variety of engineered hardwoods is available to them, including Ipe (Araucaria Angustifolia), Brazilian Cherry and Peau d'Arco.
These woods can be found online by searching for "hardwood lumber" in Google.
Do I need to be a genius to succeed in woodworking?
No. No. Woodworking isn't rocket science. Anyone can learn to use basic powertools and techniques to create beautiful work of art.
Is it possible to learn woodworking by yourself?
Learning by doing is the best way of learning anything. Woodworking requires patience, practice and skill. To master any craft, it takes time.
The best way to learn how to do something is actually to do it. Start small and use what you learn.
Statistics
- The U.S. Bureau of Labor Statistics (BLS) estimates that the number of jobs for woodworkers will decline by 4% between 2019 and 2029. (indeed.com)
- Woodworkers on the lower end of that spectrum, the bottom 10% to be exact, make roughly $24,000 a year, while the top 10% makes $108,000. (zippia.com)
- In 2014, there were just over 237,000 jobs for all woodworkers, with other wood product manufacturing employing 23 percent; wood kitchen cabinets and countertop manufacturing employing 21 percent. (theartcareerproject.com)
- Most woodworkers agree that lumber moisture needs to be under 10% for building furniture. (woodandshop.com)
External Links
How To
How to stain hardwood
Stain wood is a process that involves applying chemicals to the surface of wood, which changes its color. This chemical reaction changes the wood's color from white to brownish. Although oak is the most popular type of wood to stain, there are many other types that can be used.
There are many ways to stain wood surfaces. Mixing the stain in a solvent such as turpentine and spraying it onto the wood is one method. Other methods use a solution of water and dye applied directly to the wood. You can also mix stains with varnishes or paints so that they become part the finish coating.
Preparing the wood surface is the first step to staining it. To apply the stain, clean the wood completely. Sanding smoothens any scratches or rough spots. The next step is to determine the type of stain you would like to use. Penetrating stains are different from non-penetrating. Penetrating stains penetrate deeper into the wood than non-penetrating ones, making them ideal for dark colors such as mahogany. Penetrating stains are best paired with lighter colors, such as maple.
You will need to decide on the type of stain you want to use, and then prepare your tools. You can use a paintbrush to apply stains. This allows you spread the liquid evenly over the surface. To remove any stains left behind after painting, you will need some rags. If you intend to mix the stain yourself you will need enough containers to hold all the components.
After you have prepared your materials for staining, clean the area. You can remove grime and dirt with warm water and soap. Use a dampened sponge and warm water to clean the entire piece. Take care to remove all debris and dirt, especially if you are planning on staining darker wood.
The stain should be applied next. Start at one end of the piece of furniture and brush or spray the stain onto the wood. Slowly and carefully work your way along the grain to reach the opposite end. Make sure that the stain does not drip off the edge of the wood. Before moving on to the next steps, allow the stain drying completely.
To protect the painted surface, apply a coat of clear polyurethane sealant. Three coats are recommended for polyurethane. Allow the third coat to dry overnight before sanding the final coat.