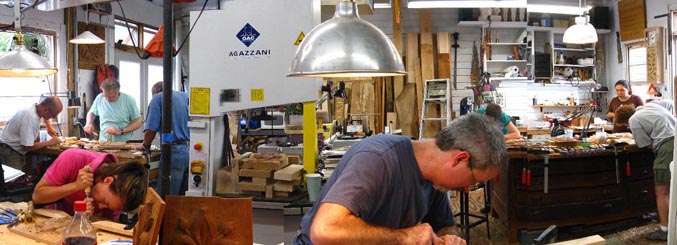
Select a piece of wood to begin carving a face out of wood. Make the necessary cuts. Using a step-by-step video, follow along as the expert guides you through the process. The progressing cut will make carving the face much more realistic. It is important to create a lifelike facial expression by adjusting the position of the noses in the wood. To create a lifelike finish, you can use colored dyes or shellac.
Hardwoods
Before carving a face out of wood, it is important to consider what type of wood you will be using. Hardwoods can be described as a group of trees with large leaves that can thrive in many climate zones. Because of their wide range of density, strength, and appearance, hardwoods are suited for various purposes, including building and furniture. While hardwoods may be more affordable than softwoods due to their durability and fire resistance, they are still very durable.
It's a good idea to use softwood if you're just starting wood carving. These woods are much easier to work with and are good for beginners. Be aware that softer woods won't have the same finish and quality as hardwoods. You should experiment with different types before you settle on a single type.
Softwoods
First, choose the type of softwood you want to use when carving a wood face. Softwoods are often more difficult to carve and have more knots. They can also be more fragile if you use long strokes. A beginner carver will frequently cut off small pieces of wood, reducing detail. It is not a problem but something to be aware.
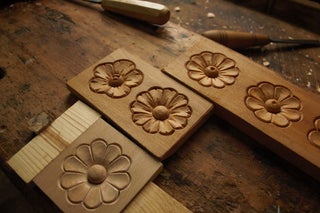
Some hardwoods can be more difficult than others. Aspen, butternut, and basswood are among the easiest to work with. You should use knives that have a greater bevel. Softwoods also make it easier to work with than hardwoods. This allows you to carve along or against the grain. The quality of your finished product will depend on the wood you choose for carving.
Colored dyes
You can create a bright, detailed finish to a wood carving by using colored dyes. These dyes are available in a variety colors that can be mixed with water or alcohol to create unique colours. You can mix colored dyes with shellac to make lighter woods. Be sure to ventilate your workspace and use denatured alcohol to clean brushes after applying the dyes. You can also use paste wax. An excessive level of glossiness may cause distractions to your work. Use 0000 steelwool to get rid of any excess glossiness.
There are many types of wood dyes that can be used and they are easy to apply. Wood dyes are compatible all topcoats, and they are easy to use. They can solve common finishing problems. They come in a variety primary colors so they are easy to mix up and apply. You can also mix and match them to your liking. You can mix them to make unique colors.
Shellac
Shellac is a product that can be applied to wood carvings. Make sure you have it handy. You can purchase a jar of shellac, but the easiest way to apply it is to use a brush. A two-pound cut should suffice. It will slowly build up and reduce brush marks. Because shellac is very thin, it is best to purchase a thicker than a thinner cut. Make your own pad out of small pieces of cotton and lintfree cloth. This will ensure you get the right amount. After that, dip the tip end of your brush in the shellac.
Shellac can be used for accenting grain or adding color. Shellac can be mixed with different colors to create custom blends. The lac can be used to darken the color. Shellac is not like other wood finishes. It won't become yellowed or cloudy over time. You can also make more faces with it because it lasts longer. And you can do this with any kind of wood carving project!
Gouges
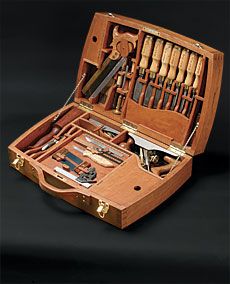
There are many sizes and shapes of gouges. Straight and palm gouges are two of the most popular types. Palm gouges can be held in one hand, while straight gouges require a larger handle and shaft. Hand held carving becomes much easier when the handles are shorter. Palm gouges also known as veiners are excellent for carving faces in wooden wood. Here are a few things to consider before you start carving.
First, learn how to choose the best gouge. You should be able cut a narrow v-shaped groove with the gouge that you select. You should ensure that you get a sharp edge with a small sweep. Gouges are often categorized according to their size. A 3/10 gouge will make the same-size cut as a 5/10 gouge. The scoop between the edges gets deeper as the first number is increased and the sweep becomes more curvy. A small-sized gouge will be capable of carving a shallow profile.
FAQ
What is the minimum investment a hobbyist needs to make in order to get started?
You will need capital to purchase the tools and supplies you need to start your woodworking business. You can start by purchasing a small table saw and drill press as well as a circular saw, circular saw, jigsaw and sanding machines. These items aren't very expensive, so you won't break the bank.
Does it take a genius to make woodworking work?
No. Woodworking is not difficult. You can create beautiful pieces of art by learning how to use simple power tools.
Can this be a way to make money?
Yes! In fact, most woodworkers already have it. According to the U.S. Bureau of Labor Statistics in May 2012, the median annual income for woodworkers was $34,000 This is more than the national average of 31,000 per annum.
Is it possible to learn woodworking by yourself?
Doing is the best way to learn any subject. Woodworking requires patience, practice and skill. Every craft takes practice and patience.
It is the best way to learn to do something is to actually do it. Start small, and work your way up from there.
How do I get started with woodworking?
You can learn the most effective way to build furniture by actually building it. You will need tools. There are bound to be mistakes. But if your persistence is consistent, you will soon master the craft.
You should first choose the project you wish to complete. It can be something as simple and small as a box, or large-scale as an entertainment center. Once you've settled on a project find a local skilled woodworker. Ask them for suggestions on the tools you will need and where to buy them. It's possible to ask your friend if they do this type of work.
Statistics
- Woodworkers on the lower end of that spectrum, the bottom 10% to be exact, make roughly $24,000 a year, while the top 10% makes $108,000. (zippia.com)
- In 2014, there were just over 237,000 jobs for all woodworkers, with other wood product manufacturing employing 23 percent; wood kitchen cabinets and countertop manufacturing employing 21 percent. (theartcareerproject.com)
- The best-paid 10 percent make $76,000, while the lowest-paid 10 percent make $34,000. (zippia.com)
- Overall employment of woodworkers is projected to grow 8 percent from 2020 to 2030, about as fast as the average for all occupations. (bls.gov)
External Links
How To
How to join wood with no nails
Woodworking is a popular hobby. Woodworking is a relaxing hobby that allows you to use your hands to create useful things from wood. There are times when two pieces of wood need to be joined together. This article will explain how to do this so that your woodwork projects stay beautiful.
First, remove any sharp edges from the wood pieces before you join them. You don't want to leave sharp corners that could cause problems later on down the road. Once you have done that, you can begin gluing your boards together.
You should only glue one side of hardwood. You should glue both sides if you are working with softwoods such as pine and cedar. Apply the glue to the boards and press them down until they are securely attached. After applying the glue, let dry the boards before proceeding to the next stage.
After you've glued your boards, you'll want to drill holes into the joints where you plan to insert screws. Depending on the type of screw that you use, the size of these holes will vary. For example, if you're going to use a 1/2-inch wood screw, then you should drill a hole that is at least 3/4 inches deep.
After drilling the holes, you can drive the screws into your board's backside. Do not hit the boards' front surfaces. It will ruin the finish. Don't drive the screws too far into the end. This will prevent splitting the wood's end grain.
Now that your project is finished, you'll want to protect it from the elements. You have two options: seal the whole furniture piece or just the top. It doesn't matter what method you use, you want something that will last many years. Oil-based varnishes are, among others, polyurethanes shellac, laquer, and other oil-based products.
These products are available at most home improvement stores. Just make sure that you buy the right kind for the job. Also, remember that some finishes are toxic and should never be used indoors. Wear protective gear whenever you are handling them.