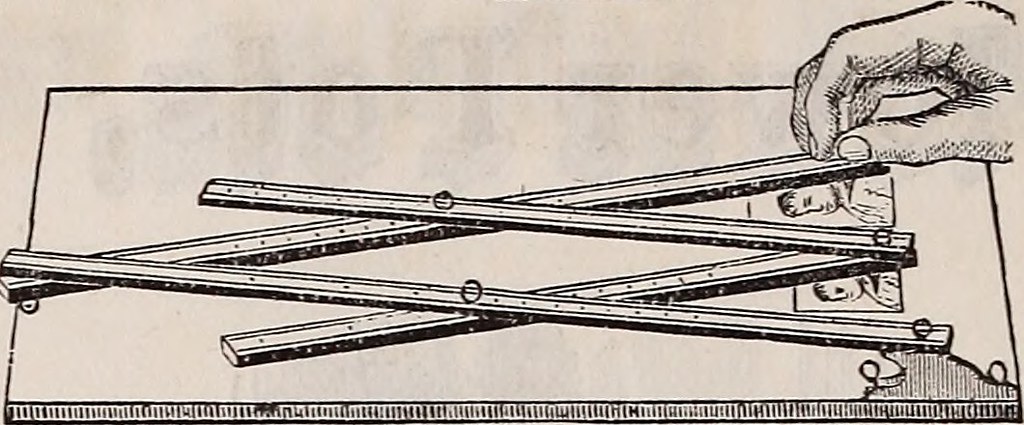
It is vital to correctly tension your bandsaw blade when you are setting it up. There are many things to consider when setting up a band saw. Your final cut will be affected by how it is set up. Follow these steps to set up a band saw, and you'll soon be cutting away! Listed below are some tips that will help you maximize your band saw's potential. Although they may seem complicated at first, these tips are definitely worth the effort in the end.
Set up a bandsaw using a tension gauge
Using a tension meter to set the bandsaw will help you get the most accurate and consistent blade tension. Read the manufacturer's instructions before you begin to cut wood. These instructions may vary slightly depending on the model. Turn the tensionwheel down 1/4 to 1/2 turn. After you have achieved this, adjust the blade guides to the recommended FSR.
To check the tension of your bandsaw blade, you can deflect it and listen for a sound. A tension meter is a costly and precise tool that allows you to adjust the blade tension to achieve maximum blade life. While a tension meter might cost you $400 or more, it is definitely worth it. If you're unsure whether you want to purchase a tensionmeter, you can always check the blade tension using a gauge.
You can check the blade tension by using a gauge
It is important to use a gauge when setting up your band saw. All blades require the exact same tension in order to cut correctly. The pulling force is usually between 200 to 800 pounds. This will determine the amount of tension you need. If you don’t own a bandsaw’s tension scale, it will give you an incorrect reading. So, what can you do?
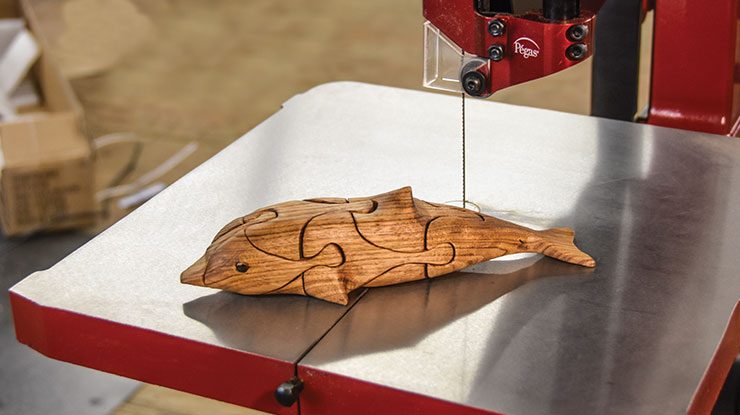
A band saw gauge is composed of two plates made from stainless steel that pivot past one another and are connected with a tensioning spring. One plate has a numeric gauge, the other a pointer indicator. The gauge is attached to the blade by three pins. Two pins sit on either side of the blade and the third pin presses against the blade on the other.
Tracking a blade
High quality cuts require proper blade setup. For a successful cut, it is crucial to have the blade set at the right height. You should set the blade height to allow for at least one-eighth to a quarter-inch clearance from your material. Excessive vibration and friction can lead to a deviation in the course of a line, so don't set your blade too high or low. You can use a tracking knob to control wobbling blades.
First, locate the blade. The blade should rest on the crown of a wheel, with its deepest part in the middle. Next, tension the blade. This tension should come from the tracking control, usually located at the back of the saw. Once the blade is in a good position, lock the control. Once you've got it right, you can begin cutting.
You can reduce drift by using a long blade
When setting up a band saw, the long blade should be positioned near the center of the crown, and the blade should not be too close to either the front or rear edge of the wheel. A blade running about an eighth-inch to quarter-inch off the center is normal. However, if your blade barely touches a wheel, you may need to adjust it. To fix this, adjust the fence and tilt the upper wheel.
It is important to have the same toe-out angle for the band saw blade as you are cutting to reduce drift. This will reduce the drift, which is the material wasted when a wood cutter starts cutting the first slice of lumber. This video will demonstrate how to properly adjust the fence angle. A jig is also an option to duplicate the fence angles.
Use a fence to align your blade
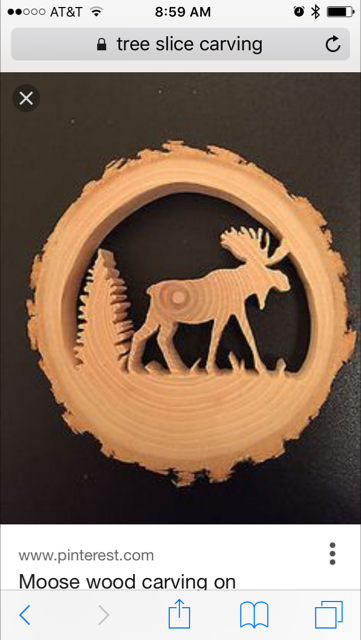
To align the band saw blade, you can use a fence. To make sure the blade is parallel with the fence, place the fence on the sidewall of the band saw closest to the fence. Then, slide the fence over the miter slot until the face of the fence is flush with the miter slot. To make sure the blade is correctly aligned, you can use your finger to push the fence over the miter slot.
Before adjusting the fence, you must set the blade guides. It is important to properly set up your band saw. The fence should be properly set up with a sharp knife. Adjusting the fence can be done to correct any deviations in the blade. A jig, or bevel square, can be used to measure the drift angle. How to do this? Watch the video. You must first determine what fence is causing the drift.
FAQ
How can a beginning woodworker make a living?
Many people are starting to learn how to build furniture because they want to start an online business. However, if you're just getting into furniture building, there are other options than selling on Etsy. Local craft fairs and events are great places to sell your products. Or you could offer workshops for others who want to learn how to build their own furniture. Perhaps you have some experience as a carpenter/builder and would like to offer your services, such as remodeling homes and creating custom pieces.
Where can I get free woodworking plans?
You don't need to purchase any books or magazines to find free woodworking plans. All you need to do is search Google. Just enter "free woodworking" into the search bar, and you'll see hundreds of websites where you can download free plans.
How do you calculate woodworking costs?
The most important thing to remember when calculating costs for any project is to keep them as low as possible. Always ensure you are getting the best possible price for materials. It's also worth taking into account all the other factors that may affect the cost of your projects, such as time, skill level, and experience. To get an idea about the average cost for common household DIY tasks, see our guide to the average woodwork project price.
What is the hourly rate for a woodworker?
The hourly rate for a professional Woodworker will vary depending on many variables, such as experience, skill level and availability.
The hourly average rate for skilled woodworkers runs between $20-$50.
A less skilled woodworker can charge as low at $10 an hour.
What woods can be used to make furniture?
Woods can be classified according to how hard they are. Softwoods include pine, fir, cedar, and cypress. Because they resist rot, softwoods can be used to make outdoor furniture. These hardwoods include maple, mahogany and teak. Because they are not weather-resistant, they are best used indoors.
How do I know what type of wood I'm dealing with?
Always inspect the label when buying wood. The label should include information about the wood species and its moisture content as well as whether or not it has been treated using preservatives.
What is the difference between a hobbyist or a professional woodworker, and how can you tell?
Hobbyists are passionate about making things from wood, while professionals tend to be more focused on the quality and craftsmanship of their work. Hobbyists often take pride in the creations they make and often share them to family and friends. Before they start working on a project, professionals will spend hours researching the designs. They will pay attention to every detail, from selecting the best materials to finishing the project perfectly.
Statistics
- Woodworkers on the lower end of that spectrum, the bottom 10% to be exact, make roughly $24,000 a year, while the top 10% makes $108,000. (zippia.com)
- Average lumber prices rose about 600 percent between April 2020 and May 2021. (familyhandyman.com)
- The best-paid 10 percent make $76,000, while the lowest-paid 10 percent make $34,000. (zippia.com)
- Most woodworkers agree that lumber moisture needs to be under 10% for building furniture. (woodandshop.com)
External Links
How To
How to join two pieces of wood together without nails
Woodworking is an enjoyable hobby. It's fun and relaxing because you can use your hands to make something useful from wood. You might want to join two pieces from the same wood, but you don't need to use nails. This article will demonstrate how to do so to preserve the beauty of your woodwork.
You will first need to trim the edges of your wood pieces before joining them. You don't want to leave sharp corners that could cause problems later on down the road. After you have completed this step, you are ready to glue your boards together.
If you are working with hardwood, only one side should be glue. If you are using softwoods such pine or cedar, glue should only be applied to one side. Once you have applied the glue, press down on the boards until they are fully attached. Before you proceed to the next step, be sure to let the glue dry completely.
After you have glued the boards together, drill holes in the joints where you intend to place screws. You can choose the type of screw to determine the size of your holes. For example, if your screw is a 1/2-inch wooden screw, drill a hole that is at minimum 3/4 inches deep.
After drilling your holes, drive the screws into the board's backside. Do not hit the boards' front surfaces. It will ruin the finish. Don't drive the screws too far into the end. This will prevent splitting in the end grain of the wood.
Now that your project is finished, you'll want to protect it from the elements. You can either seal the entire piece of furniture or cover the top. It doesn't matter what method you use, you want something that will last many years. You can choose from oil-based varnishes or polyurethane, shellac and lacquer as examples.
You can find these products at most home improvement stores. Make sure you get the right product for your job. Remember that some finishes can be toxic, so you should not use them indoors. Always wear protective gear when handling any of these finishes.