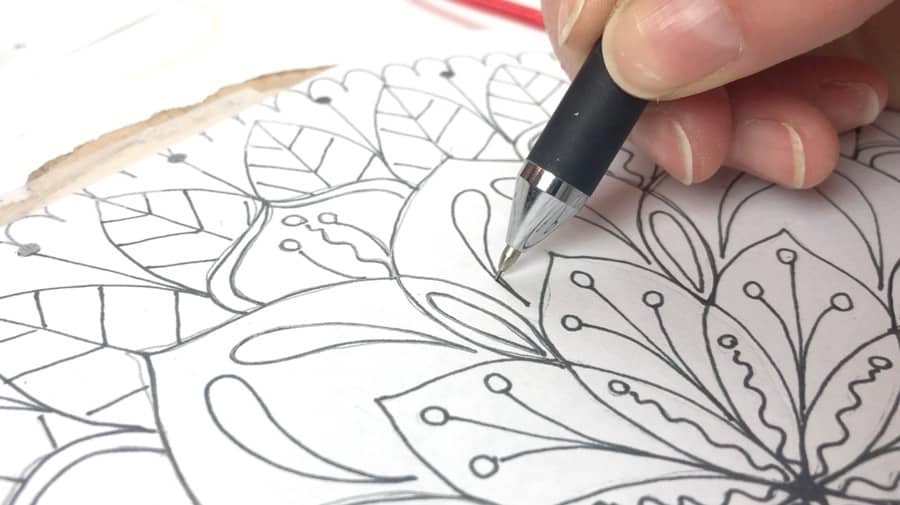
You might be asking yourself, "Why do I need a transfer tip for wood burning?" A transfer tip is the only thing that will keep you from the surface you wish to burn. A variety of products can carry a wood burning tip, including a portable base that can accommodate it. Be sure to understand how to attach a tip to a wood burning torch and how it works.
Carbon paper
When using carbon paper as a wood burning transfer tip, you need to prepare your pattern paper in advance. The first step is to fold the pattern paper in half. Next, take a soft lead pencil and rub the entire design area with it. After the transfer is completed, you can remove carbon paper and redraw the design. You can also trace your lines with an ink pen. Burning ink leaves a line so make sure you carefully follow your pattern.
While carbon paper is preferred by most buyers, some users find it difficult and cumbersome to use. Many prefer to use trace paper. It works well, but you need to be careful and not burn the paper to prevent it from tearing. The best carbon paper for wood-burning is made from traditional materials and can be reused. Carbon paper is also a time- and paper-saving tool. The carbon paper can be used for many purposes. You can usually find the carbon paper in a ziplock bag.
Photo paper
When burning a photo, you may be tempted to just burn the entire photo. You might be tempted to burn the whole photo. To make sure that the text is properly printed, mirror the image. Also, don't touch the glossy side of the photo because it can smear the ink. Chartpak colorless blend pen can be used to transfer more detailed photos. This pen can transfer detailed lines and images for $5. It is available in a range of colors and costs around $5.
If you're working with a smaller wood canvas, photo paper is a great option for transferring patterns. Photo paper is simple to find and can be used to replace messy carbon paper. Select a photo-paper that is smooth, so it doesn’t absorb the printer’s ink. Place the ink-side down on the wood and then lift it up to reveal the fully transferred image.
Razertip Transfer Shader Pyrography
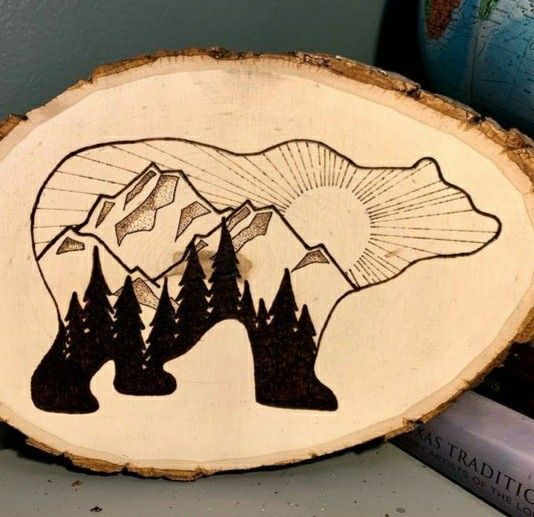
The Razertip Transfer Shader is one among the most sought-after wood burning tips. The tip is made of stainless steel and has a teardrop-shaped shape. It can be used to shade or transfer heat-photocopied patterns. There are three types of handpieces available to suit a variety projects. Razertip can also be used as a pyrography tool to create fine line. Razertip.com provides more information.
Razertip pyrography pencils come with a 1-year warranty. The pens are available with hundreds of different tip types. They are one of the most small pens currently available, making them ideal for delicate detail working. They are also designed for durability. The more durable models have thicker tips and connectors posts, larger pen bodies and are more resistant. They require a heavier cord and a higher heating set.
Graphite pencil
A tracing sheet is an essential item when using a graphite pen for wood burning transfer tips. This paper will serve as your guide when transferring a design to wood. To make your transfer process as easy as possible, you must first determine the design you want to transfer. You have the option of choosing a simple design or a more intricate one depending on what you want. A complex design may be easier to transfer by printing it first.
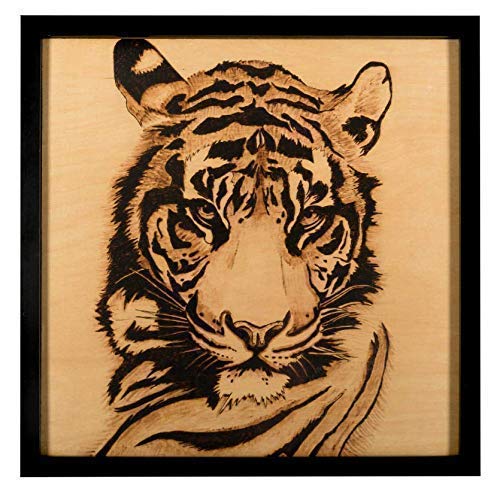
Place the graphite with the dark side facing toward the wood. Follow the design line with light to medium pressure. Once you've completed this process, remove the paper. You can now transfer the design. You can trace the design by hand if you are a beginner. This method, however, won't be as effective as using a graphite pencil because it will cause the wood to become stiff.
FAQ
What type of wood should I choose?
Woodworking is a popular job that involves oak, pine and maple. Each wood type has its own characteristics which affect the final product's appearance and feel. Oak, for instance, is darker and harder than most other woods. Birch, which is lighter and soft, is more heavy than mahogany. You also have the option of solid wood or veneers. Veneers consist of thin sheets made from wood and glued together to form a single layer.
Can I refinish furniture that I make?
Yes! You don't have to hire a professional to refinish furniture. There are many ways you can do it yourself. Here are some suggestions:
Use sandpaper for removing stains and scratches. Finally, use a clean cloth or sponge to clean the surface.
Apply clear polyurethane paint. Allow to dry thoroughly before moving furniture.
Use acrylic paint to paint furniture.
Stain can be used instead of paint. Furniture will look richer with the stain.
Apply shellac wax. Wax will protect the wood and add shine.
Is it difficult to start my woodworking business?
Starting your own woodworking business isn't easy. You will need to adhere to many legal requirements. This doesn't necessarily mean that you should go through all the work of setting up a company. Many people prefer to join existing companies. This will allow you to avoid paying membership fees and taxes.
How do I organize my shop?
Setting aside an area to store tools is the first step in keeping your workshop organized. Your tools will stay sharp and ready to go when they are free from dust and debris. Use pegboard hooks to hang tools and accessories.
Can I make a living doing this?
Yes! Many woodworkers have this ability. According to the U.S. Bureau of Labor Statistics, the median annual woodworker wage was $34,000 in May 2012. This is higher than the $31,000 annual national average.
Statistics
- If your lumber isn't as dry as you would like when you purchase it (over 22% in Glen Huey's opinion…probably over 10-15% in my opinion), then it's a good idea to let it acclimate to your workshop for a couple of weeks. (woodandshop.com)
- The best-paid 10 percent make $76,000, while the lowest-paid 10 percent make $34,000. (zippia.com)
- In 2014, there were just over 237,000 jobs for all woodworkers, with other wood product manufacturing employing 23 percent; wood kitchen cabinets and countertop manufacturing employing 21 percent. (theartcareerproject.com)
- The U.S. Bureau of Labor Statistics (BLS) estimates that the number of jobs for woodworkers will decline by 4% between 2019 and 2029. (indeed.com)
External Links
How To
How to join wood with no nails
Woodworking is a hobby that many people enjoy doing. Woodworking is a relaxing hobby that allows you to use your hands to create useful things from wood. Sometimes you may want to join two pieces together of wood without using nails. This article will explain how to do this so that your woodwork projects stay beautiful.
First, remove any sharp edges from the wood pieces before you join them. You don't want to leave sharp corners that could cause problems later on down the road. Now it's time to start glueing your boards together.
When working with hardwood, glue should be applied only to one side. For softwoods like cedar and pine, glue should be applied to both sides. After applying the glue, press the boards firmly until they are completely stuck together. Make sure you let the glue dry before moving on to the next step.
Once you've glued your boards together you will need to drill holes in the joints to accommodate screws. Depending on what type screw you choose, the size of these holes will depend on how big they are. For example, if you're going to use a 1/2-inch wood screw, then you should drill a hole that is at least 3/4 inches deep.
Once you have drilled the holes, the next step is to drive your screws through the joint into the board's backside. Avoid hitting the board's top surface. Otherwise, you could ruin the finish. When driving the screws, try to avoid hitting the ends of the screws too much. This will prevent splitting the wood's end grain.
Protect your finished project now. To do this, you can seal the entire furniture piece or just cover the top. You want it to last years, so you can use any product. Some examples include oil-based varnishes, polyurethane, shellac, lacquer, etc.
You can find these products at most home improvement stores. Make sure you get the right product for your job. Keep in mind that certain finishes can be toxic and should not be used indoors. When handling certain finishes, wear protective gear.