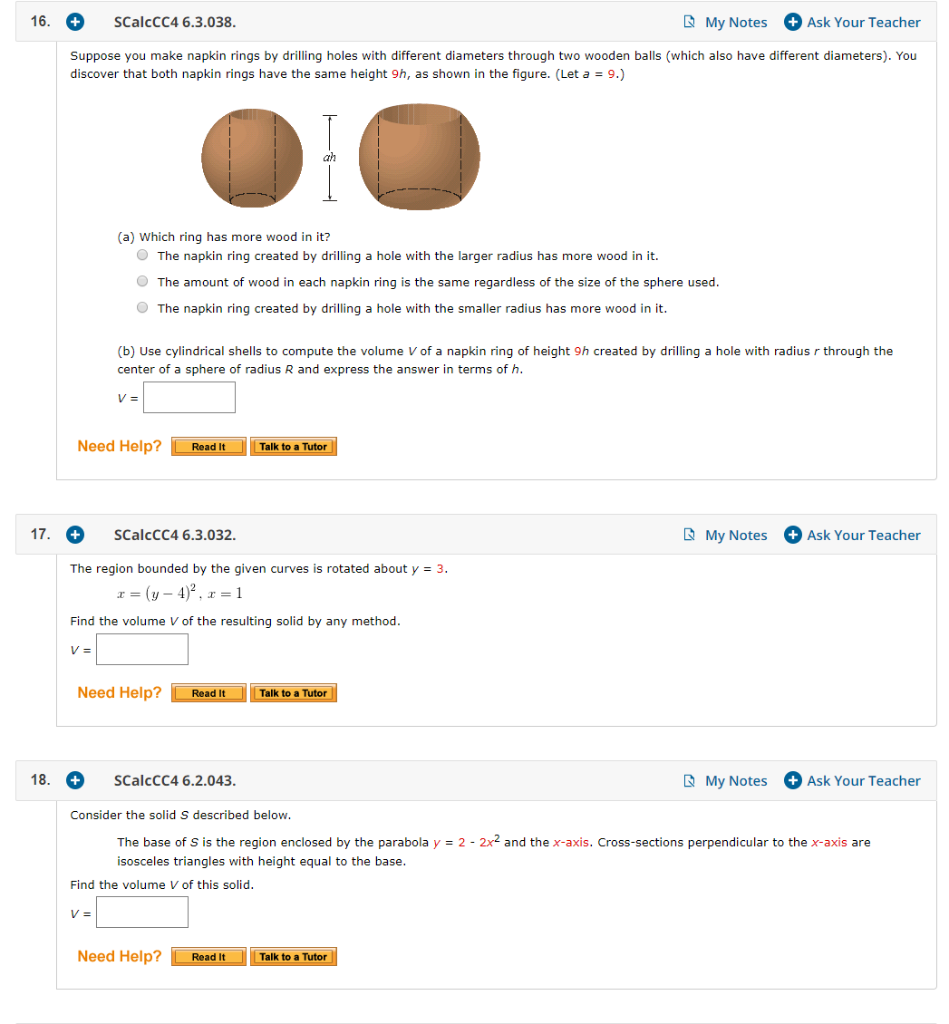
It can be difficult for rough lumber to be loaded into your car. When you visit the store, make sure you have your tape measure and hand saw. Also, make sure to buy extra boards in the event that the one you have purchased doesn't fit. Be sure to buy the board with knots and checks. It's not worth ripping a board and starting over. You will be wasting your time and money. It is better to purchase one or two more boards.
We save money!
A sawmill will typically turn 59% of the log volume into boards when it cuts rough lumber. The remainder of the log, which includes sawdust or bark, is considered waste. Even though a poor cut may result in more wasted wood, the amount should not exceed 20%. Here's an easy formula to calculate how much wood is left over after a board has been cut. For a nominal 4-foot board, the sawmill should remove about 18% of its volume to achieve the desired lumber thickness and width.
One thing is that rough lumber does not come in the same dimensions. The dimensions for hardwood bought at big box stores are often known so you can plan your project around that size. The rough edges of lumber can be uneven, which leads to wasted material. The common width of rough-cut lumber can lead to a lot waste. These wastes can't be recycled later.
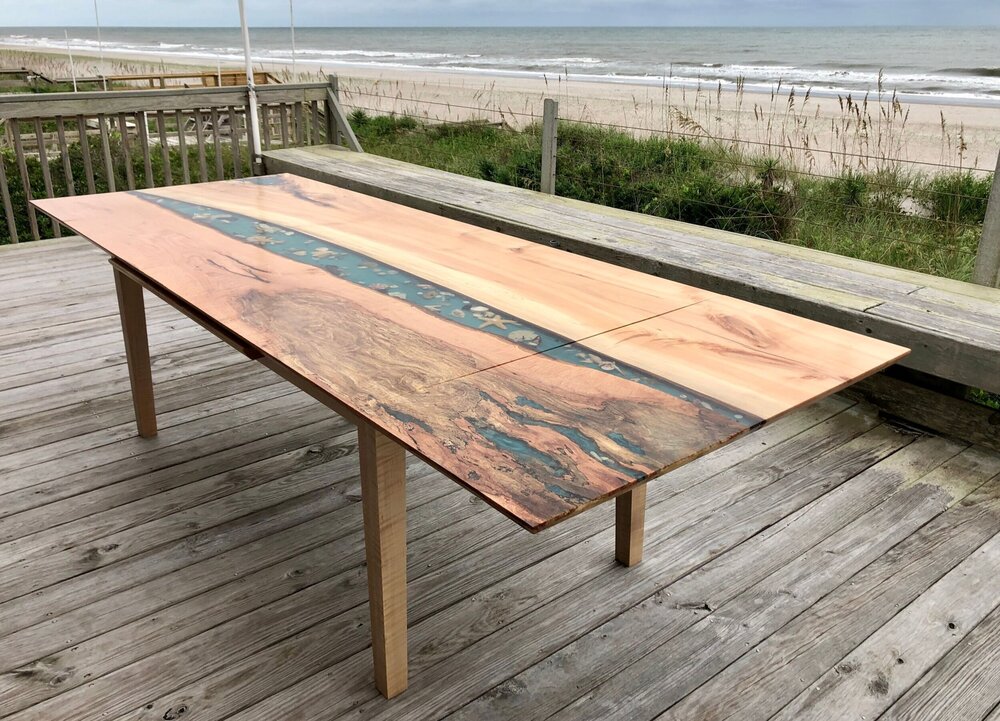
Preparation
To prepare for cutting rough lumber, the first step is to measure the length. Rough lumber may not be perfectly flat when it arrives from the lumber yard. It may not be perfectly flat and have uneven edges and faces. Therefore, it may take multiple passes to flatten. As a rule of thumb, you should remove 1/16 inch per pass. Run the lumber through the saw with concave surfaces.
The rough cut lumber should generally be flattened to 1/4" before the saw cuts. After flattening your face, plane the board to the desired thickness. Measure the length and width of the finished lumber once you have determined the thickness. Don't forget to consider any imperfections. Be sure to leave a minimum of one-quarter inch space on each side of the board. You can also plan your project using the available boards. Do not buy lumber that is uneven. It will be difficult to work on boards that are bowed, warped or twisted.
Prices
There are two types. Dimensional lumber and rough-sawn. Home improvement stores generally carry finished lumber but very rarely rough-sawn. Both types of lumber are often available at local sawmills and lumber yards. The difference between the two types is in the amount of work required to process them. A rough-sawn board is a more affordable option because it requires less processing. It is also thinner and wider than finished lumber.
While buying lumber from a yard or mill is cheaper, you are less likely than others to find it in standard lengths. Milling your own lumber can be a cost-effective alternative to buying rough-sawn lumber, though you'll need shop space and upgraded power. You will need to be trained and it can be very noisy. If you plan to use your mill, you may want to consider zoning laws in your area.
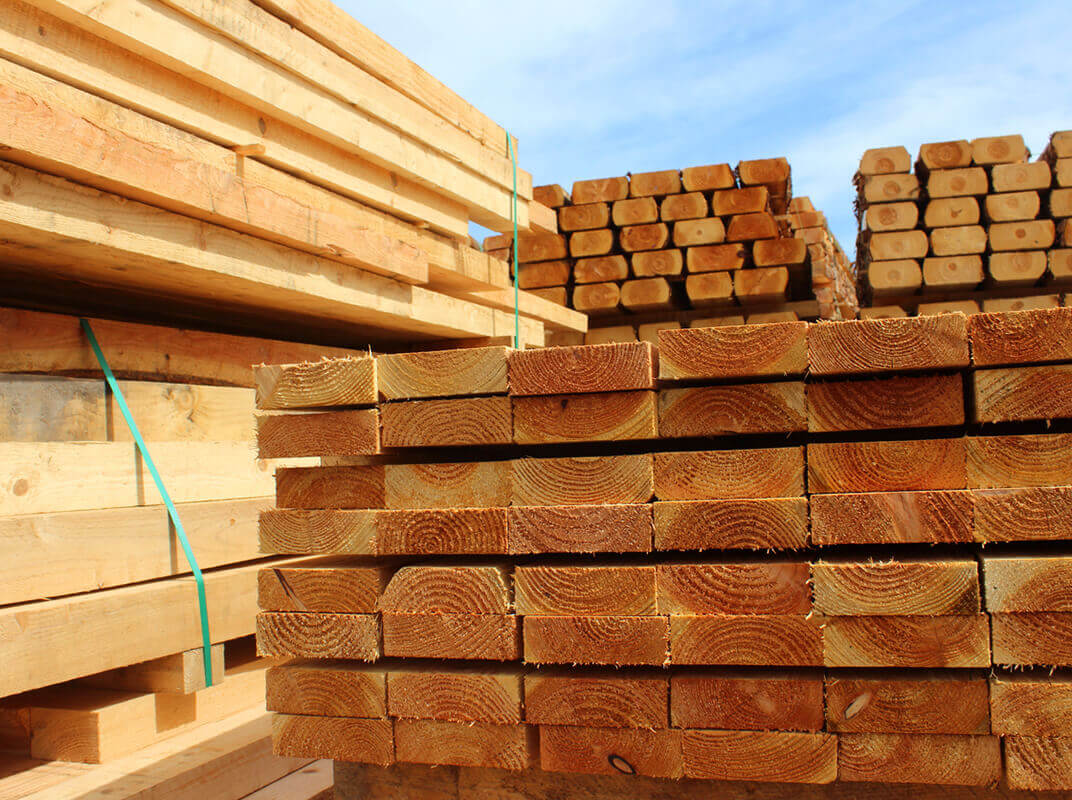
Source
When buying lumber, you have a number of options. There are many different sizes, shapes or finishes that you can choose from. Rough sawn lumber, by example, is unfinished lumber. It has been cut into boards. This lumber is stronger than the other types due to its higher moisture content. However, it is thicker than standard surfaced wood. These are some of the advantages you have when using rough sawn timber for your woodworking projects.
The first is the availability and low cost. Rough lumber is not treated and is not usually sold at a hardware store. But, rough lumber has its benefits and drawbacks. Although it is less expensive per board foot, it is more expensive to transport. It takes longer to finish than treated wood. This is why you might consider it when deciding on how much lumber you want to purchase. Consider purchasing large quantities of rough sawn lumber and small amounts for finishing if you intend to use it for your project.
FAQ
How can I learn basic woodworking skills
The best way to learn how furniture construction is to make your own bench. This project can easily be done using whatever wood you have at your house. If you're not sure which kind of wood to choose, you can purchase cheap pine boards at Lowes and Home Depot. After building your bench, sand off any rough edges and apply a stain or varnish.
How do I get started with woodworking?
You can learn the most effective way to build furniture by actually building it. You'll need tools, and you'll have to make mistakes along the way, but if you keep at it, you'll eventually figure out what you're doing.
Begin by choosing the project that you want to finish. It can be something as simple and small as a box, or large-scale as an entertainment center. After you have decided on a project to work on, contact a local woodworker that specializes in this type of work. Ask the local woodworker for help in deciding what tools and where to get them. Maybe you can ask the person if they know of anyone who does this sort of work.
Which material would you recommend for woodworking lessons?
You can start with softwoods like pine or poplar. You will feel more comfortable with these softwoods, so you can move onto hardwood.
Statistics
- In 2014, there were just over 237,000 jobs for all woodworkers, with other wood product manufacturing employing 23 percent; wood kitchen cabinets and countertop manufacturing employing 21 percent. (theartcareerproject.com)
- The U.S. Bureau of Labor Statistics (BLS) estimates that the number of jobs for woodworkers will decline by 4% between 2019 and 2029. (indeed.com)
- Most woodworkers agree that lumber moisture needs to be under 10% for building furniture. (woodandshop.com)
- The best-paid 10 percent make $76,000, while the lowest-paid 10 percent make $34,000. (zippia.com)
External Links
How To
How to stain wood
Stain wood is a process that involves applying chemicals to the surface of wood, which changes its color. This chemical reaction causes wood to turn from whiteish to brownish. The most common type of wood used for staining is oak, although many other types of wood can be stained.
There are many methods to apply stain to wood surfaces. Some methods include mixing the stain along with a solvent like turpentine and then applying the mixture to the wood by brushing or spraying. Others use a solution made up of water and dye, which is then applied directly onto the wood. The stain can be mixed with paints and varnishes to become part of the final coating.
Preparing the wood surface is the first step to staining it. Clean the wood to get rid of any grease, dirt or other substances that might be detrimental to the stain's application. Sanding the wood smooths out rough spots and scratches. Next, you need to decide which stain you want. There are two basic kinds of stains: penetrating stains and non-penetrating stains. Penetrating stains penetrate deeper into the wood than non-penetrating ones, making them ideal for dark colors such as mahogany. Penetrating stains are best paired with lighter colors, such as maple.
After choosing the type and application method you prefer, gather your tools. You can use a paintbrush to apply stains. This allows you spread the liquid evenly over the surface. You should also have some handy rags to wipe up excess stains after you finish painting. If you intend to mix the stain yourself you will need enough containers to hold all the components.
Once you have prepared all your materials, it is time to clean the areas where you will stain the wood. Clean the area with soap and warm water to get rid of dirt and grime. Use a dampened sponge and warm water to clean the entire piece. You should remove any debris, especially if your plan is to stain darker wood.
The stain should be applied next. Next, apply the stain to the furniture by starting at one end. Slowly and carefully work your way along the grain to reach the opposite end. Make sure that the stain does not drip off the edge of the wood. Before moving on to the next steps, allow the stain drying completely.
To protect the painted surface, apply a coat of clear polyurethane sealant. Three coats are recommended for polyurethane. Allow the third coat of polyurethane sealer to dry overnight before applying the final coat.