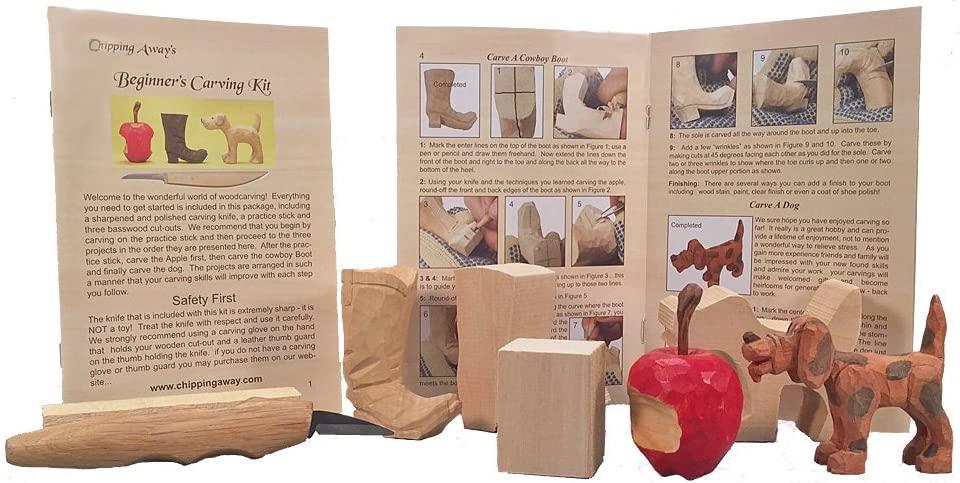
Chip carving can be difficult if you've ever tried it. There are many styles and techniques you can use, but which one is the best? What tools are necessary? This article will give you my top tips and tricks when carving chips. There are many essentials to chip carving success, regardless of whether you prefer traditional or modern style.
Traditional
Chip carving is one the oldest forms decorative woodcarving. It requires a straight-edged knife but a skew-ground or offset blade knife can also be used. Chip carving is a technique that involves making small, triangular incisions into wood in order to create a pattern. This art form was developed simultaneously in several countries and dates back over 1000 years. The designs are often so similar that it was difficult to distinguish between them because of their popularity.
The skills needed to carve wood became more popular as the practice spread around the globe. Chip carving was an art form used to decorate furniture in Sweden. Schools were created to teach the art. Modern chip carvers have benefitted from the skills and knowledge of centuries-old carvers. Through generations, the knowledge and experience of carvers was passed on from apprentice to student. It is a process that lasts a lifetime and continues to this day.
Formulary free
If you've always wanted to try chip carving, you've come to the right place. Murray Taylor has created a DVD that shows you how create both freeform and geometric carvings. It's an excellent introduction project that contains lots of information. English and NTSC versions of the DVD are available. The DVD can be purchased in stereo or widescreen. The owner of the DVD is Artisan Media Ltd., and it is available in MP4 format for Windows and Mac computers.
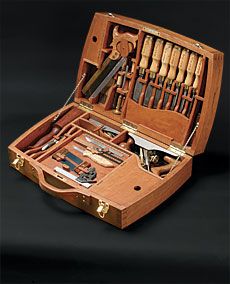
Triangles, circles and lines are the basic shapes of geometric chip carving. This technique can be combined with different styles and shapes to create endless possibilities. This style of chip carving is also referred to as free form chip carving. It doesn't matter if you want your chips to look like a flower or a dragon. They will make a great addition to any room. The best way to incorporate different techniques into one piece is by freeform chip carving.
Techniques
Chip carving has been around since the beginning of time. Examples can be found in countless countries throughout the world. Chip carvings have been discovered on paddles and handles for ceremonial tools in the South Pacific Islands. These carvings were most likely done using bits of bone and sea shells, but some people have reported using shark teeth as well. This book shows you how to create beautiful designs with a variety of chip-carving techniques.
You can easily carve chip if your follow some basic steps. The first of these is to know how to carve the fine triangle. This pattern is very easy to comprehend and execute. To carve this pattern you will simply need to make several triangles. Then, repeat this process. It doesn't have to be boring. Simply by changing the angles, you can create amazing patterns.
Tools
Lora Irish offers an online seminar for free that will cover the basics of chip-carving. She shows you how to use a variety of carving tools and materials, such as a chip, stab, and detail knife. In this free seminar, Irish also covers the different types of wood carving tools. To purchase the right tool, you can choose from this list. These tools can be used to create simple designs and shapes, or more complex designs.
Special geometry is required for chip carving knives. It is approximately 1 1/2 inches long with a narrow back edge. This makes it easy to make precise cuts. You should also choose a point that is sharp and needle-sharp so that the edges meet perfectly. Chip carving knives are also made of stainless steel and come with a sharp tip. A chip carving knife should have a sharp tip that can cut through a piece of wood.
Getting started
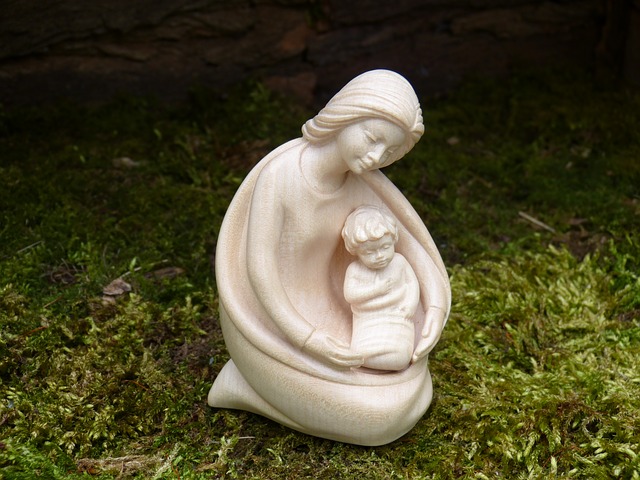
It is essential to learn about the methodology of chip carving before you begin. The process will vary depending on what type of carving you are doing. To make your work as accurate and precise as possible, it is important that you are familiar with these basic principles. Chip carving involves making a fine cut in the wood. To create your first chip carving, follow these steps:
When using a chip carving knife, it is essential to sharpen it well. A chip carving knife's blade will have bevels at each end. This indicates that it is primary. The sharpening rock is shaped as a diamond, and can produce effective edges. Place the stone at a 10 degree angle. It will also sharpen your chip carving knife as well as your chip carving tool simultaneously.
FAQ
Is there a way to start my own woodworking company?
It is not easy to start a woodworking business. There are many regulations and legal requirements that you will need to comply with. You don't have to go through all that hassle of setting it up. Many people decide to join established businesses. You only need to pay membership and tax fees.
How often do I need to buy new supplies
Over time, you may need to replace your tools. You'll need to sharpen your hand tools regularly if you use them. If you are using power tools, you will need to purchase replacement parts regularly. Try spreading your purchases over a few months so you don't buy too many at once.
What would be your first step in woodworking?
You can start with softwoods like pine or poplar. You will feel more comfortable with these softwoods, so you can move onto hardwood.
How much should a hobbyist invest to get started?
It is likely that you will need some capital in order to buy the required tools and supplies if your goal is to open your own woodworking business. A good place to start would be by buying a small table saw, drill press, circular saw, jigsaw, and sanding machine. These items don't cost much so they won't break your budget.
How do I get started as a woodworker?
Woodworking requires patience and practice. It takes time and practice to master the various techniques and tools required for woodworking.
There are many options for woodworking equipment today. Some prefer to use power tools and others prefer hand tools.
Your choice, however, is up to you. However, you need to ensure that the tool you use is the right one for the job. You might start with a simple set of tools if you don't have much experience.
You might also consider learning how to use the router to create intricate shapes from wood. You can find these at most hardware stores.
What is the difference in a hobbyist and professional woodworker?
Hobbyists love making things from wood while professionals are more concerned with the quality of their work. Hobbyists often take pride in the creations they make and often share them to family and friends. Professionals will spend hours looking at designs before they start to build a project. They'll pay great attention to details, from choosing the most suitable materials to finishing the work perfectly.
Statistics
- The best-paid 10 percent make $76,000, while the lowest-paid 10 percent make $34,000. (zippia.com)
- If your lumber isn't as dry as you would like when you purchase it (over 22% in Glen Huey's opinion…probably over 10-15% in my opinion), then it's a good idea to let it acclimate to your workshop for a couple of weeks. (woodandshop.com)
- The U.S. Bureau of Labor Statistics (BLS) estimates that the number of jobs for woodworkers will decline by 4% between 2019 and 2029. (indeed.com)
- Overall employment of woodworkers is projected to grow 8 percent from 2020 to 2030, about as fast as the average for all occupations. (bls.gov)
External Links
How To
How to make wood joint
This tutorial will teach you how to join two pieces wood together. We will be using the "pocket-hole joint", which involves drilling holes in wood and then gluing them together. If your wood is straight and flat, this method will work well. Try dowel joinery instead if your wood doesn't look straight. Here are the steps
-
Drill Pocket Hole Joints. To start, measure and mark where you want to put the pocket hole joint. Then drill 3/4 inch deep holes into the ends of each piece of wood using a jig saw or handheld drilling machine.
-
Sand Smooth. Sanding the wood's edges will ensure that the joint doesn't split.
-
Glue Together Apply glue to the sides of both wood. Allow it to cool for at least 5 minutes before you attach the pieces.
-
Secure the pieces together. After the glue has dried you can attach the pieces to form a flush joint.
-
Trim Joinery. Trim any excess wood surrounding the joint once the glue has dried completely.
To be able to turn the pieces inside-out, leave enough room between them.