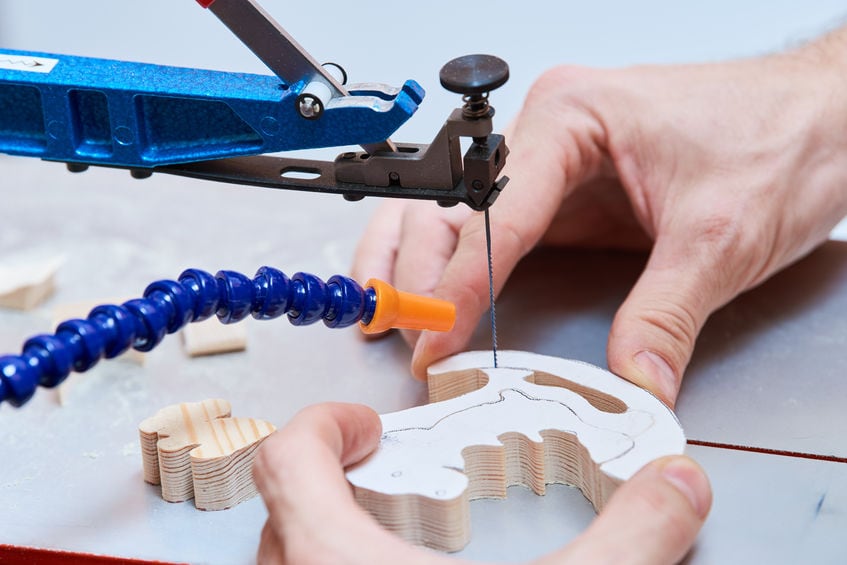
It is vital to correctly tension your bandsaw blade when you are setting it up. There are many things to consider when setting up a band saw. Your final cut will be affected by how it is set up. You'll soon be cutting with ease if you follow these steps to set-up a bandsaw. Here are some tips for maximising the potential of your saw. Although they may seem complicated at first, these tips are definitely worth the effort in the end.
Set up a bandsaw using a tension gauge
You can get the most consistent and accurate blade tension by using a tension gauge to set your bandsaw. You should carefully read the instructions before you begin cutting wood. These instructions can vary depending on which model you have. To begin, turn the tensionwheel down by a quarter-to-half turn. Once you have done this, you can adjust the FSR of your blade guides.
A second way to check the tension on a bandsaw is to deflect your blade and listen for an audible tone. A tension meter is an expensive and accurate tool that will allow you to adjust the blade tension for maximum blade life. While a tension meter might cost you $400 or more, it is definitely worth it. You don't have to buy a tension meter if you don't want one. A gauge can be used to check the tension of your blades.
Using a gauge to check blade tension
Using a gauge when setting up a band saw is critical, as all blades require the same amount of tension to cut properly. The pulling force, generally between 200-800 pounds, will dictate the tension. If you don't have a bandsaw, a tension scale can give you inaccurate readings. So, what can you do?
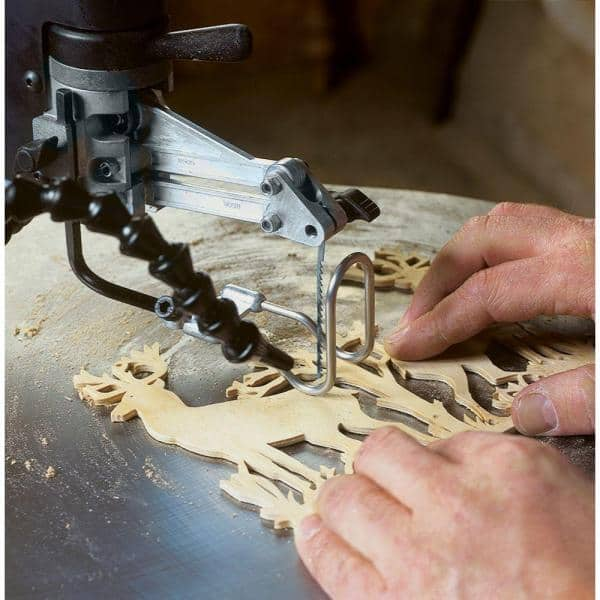
A bandsaw gauge is composed two stainless steel plates which pivot past each others and are connected using a tensioning Spring. The numeric scale on one plate is visible, while the pointer indicator can be found on the other. The gauge attaches to the blade using three pins. The gauge is attached to the blade with two pins on each side. The third pin presses against one end of the blade.
Follow a blade
Proper blade setup is crucial for achieving quality cuts. For a successful cut, it is crucial to have the blade set at the right height. You should set the blade height to allow for at least one-eighth to a quarter-inch clearance from your material. Too low or too high blade height will cause excessive vibration and friction and head off course when following a line. You can use a tracking knob to control wobbling blades.
First, locate the blade. The blade should rest on the crown of a wheel, with its deepest part in the middle. Next, tension the blade. The tracking control is usually located at the back. This tension should be applied to the blade. After the blade has been placed correctly, lock the control. Once you have the blade in place, you can cut.
Using a long blade to reduce drift
A band saw's long blade should be located near the center of its crown. The blade should not be too close either to the front or rear edges of the wheel. A typical blade will not be too far off center by about an eighth to quarter of an inch. However, if the blade is barely touching the wheel it may need some adjustments. Adjust the fence and tilt your upper wheel to fix this.
The best way to account for drift when setting up a band saw is to use a long blade with the same toe-out angle as the blade you are cutting. This will reduce drift, which refers to the material lost when the wood cutter cuts the first slice. In the video below you will see one method to properly set the fence angle. A jig is also an option to duplicate the fence angles.
Using a fence to align the blade
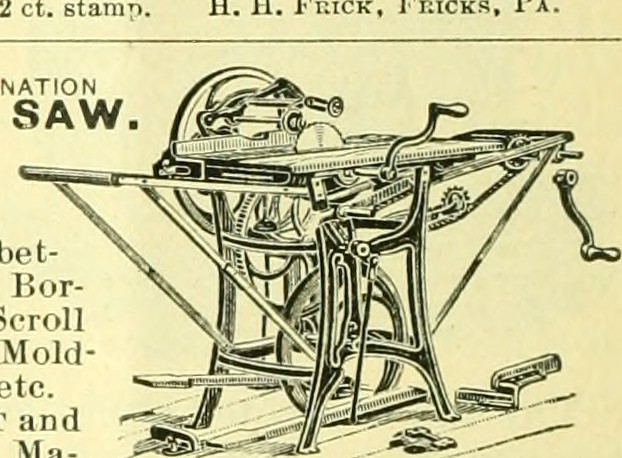
The alignment of the blade on a bandsaw is simple by using a fence. The fence should be placed on the fence closest to the fence. Slide the fence over the miter slots until the fence's face is flush with it. A finger may be used to align the blade properly.
Before you can adjust the fence, it is important to place the blade guides. You must properly set up the band saw. You must place the fence with a sharp blade. You must adjust the fence to compensate for any drifting of the blade. To measure the drift angle, you can use a jig or a bevel square. How to do this? Watch the video. First, determine what fence is causing drift.
FAQ
What wooden items do you sell well?
The most successful wooden items are made from sustainable wood.
Most furniture is made from oak, maple, mahogany or walnut.
These woods are extremely strong but also have beautiful colors and grain patterns. They can also last for years if they are properly cared for.
Wooden furniture should always be painted first to protect against moisture damage. This applies to all surfaces including drawers, doors, handles, and handles.
Choose a paint with water resistance if you want furniture to last as long possible.
A high-quality oil-based primer should be used, followed by two coats with top coat. You may need to apply several coats of top coat depending on how much wear it is expected.
You should avoid using aerosol paints or spray cans. These products contain solvents that evaporate quickly and leave behind harmful fumes.
What kind of tools do carpenters use?
Carpenters use a hammer as their most common tool. A hammer helps to carpenter pound nails into the wood. They can also use it to hold the pieces together as they work on a project. Other tools include clamps. pliers. screwdrivers. measuring tape. pencils. saws. drills. wrenches.
How much does a hobbyist need to invest in getting started?
To start your own woodworking company, you will likely need capital to purchase the necessary tools and other supplies. It's a good idea to buy a small tablesaw, drill press and circular saw. These items don't cost much so they won't break your budget.
Statistics
- If your lumber isn't as dry as you would like when you purchase it (over 22% in Glen Huey's opinion…probably over 10-15% in my opinion), then it's a good idea to let it acclimate to your workshop for a couple of weeks. (woodandshop.com)
- The best-paid 10 percent make $76,000, while the lowest-paid 10 percent make $34,000. (zippia.com)
- Most woodworkers agree that lumber moisture needs to be under 10% for building furniture. (woodandshop.com)
- Overall employment of woodworkers is projected to grow 8 percent from 2020 to 2030, about as fast as the average for all occupations. (bls.gov)
External Links
How To
How to make wood joints
This tutorial will help you join two pieces of wooden together. We will use the "pockethole joint," which means that we drill holes in the wooden pieces and then glue them together. This works well if the wood is straight and smooth. You may want to consider other methods, such as dowel joining. These are the steps
-
Drill Pocket Hole Joints. Start by measuring and marking the spot where the pocket hole joint will be placed. Next, drill 3/4 inch holes in each end of each piece using a handheld drilling machine or jigsaw.
-
Sand Smooth. You can sand the edges of the wood to ensure that it doesn't split.
-
Glue Together Apply glue to both ends of the wood. Let it sit for about 5 minutes before clamping the pieces together.
-
Fix the Pieces together. After the glue has dried thoroughly, secure the pieces so that they are flush.
-
Trim Joinery. Trim the excess wood around the joint after the glue has dried completely.
Be sure to leave enough space between each piece so that they can be turned inside-out.